Tower Raising
June, 2025
I had no trouble putting up the first 10′ of tower and stringing the temporary guy wires. The challenge was going to be finding some helpers to work on the ground, doing the hard work of waiting and pulling.
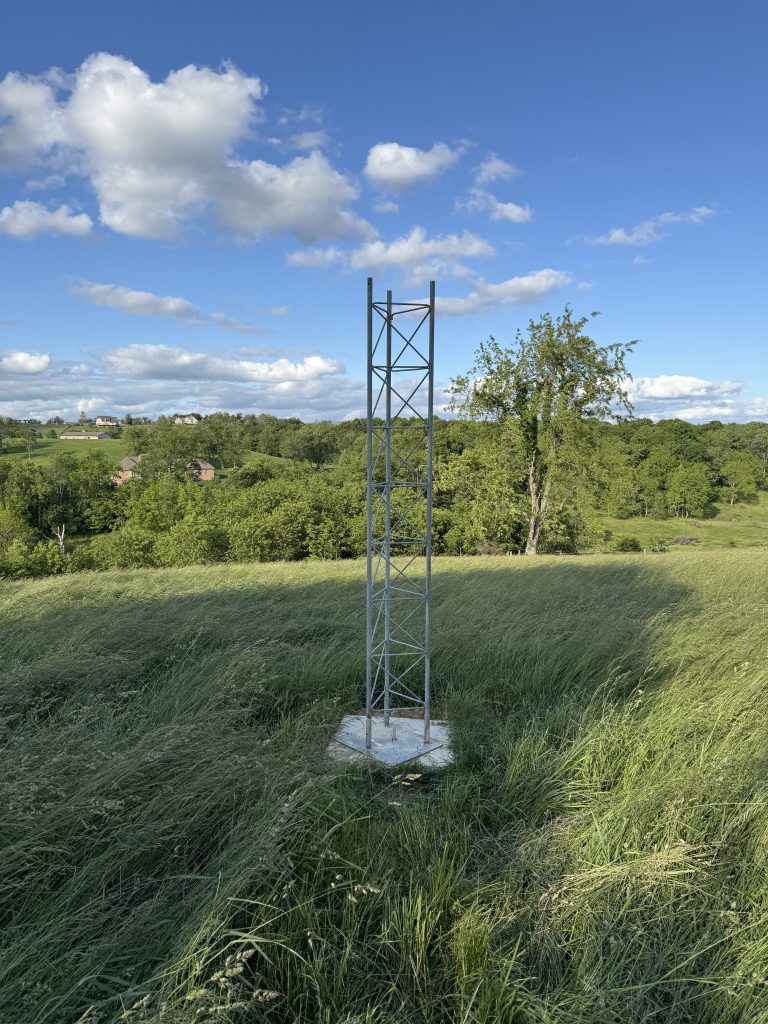
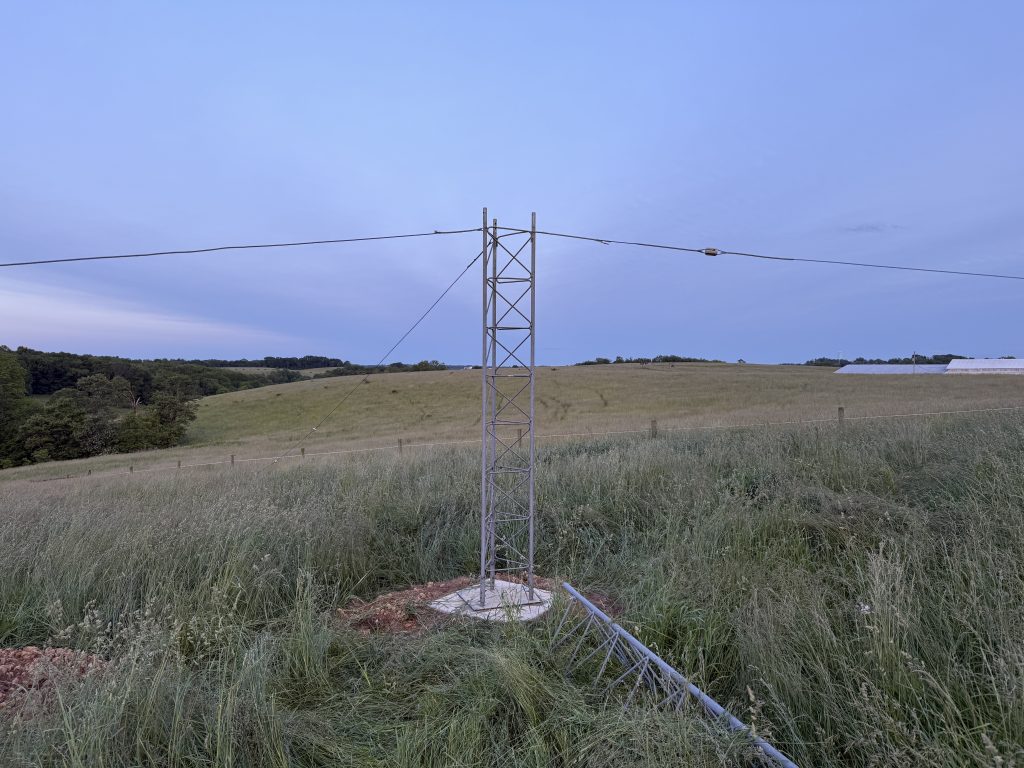
On one of the Q5 Contest Crew episodes, I was reporting on the station building progress and mentioned that I needed to find some ground crew. I was pleasantly surprised when several people contacted me to offer their help. The big break happened the week before Field Day when I was introduced to Mike WA3C via Contest Crew fan Tom KF8AVC. Mike has a multi-tower station of his own, considerable tower experience, and lives just 45 minutes away. He very generously offered to come over and help.
In addition to his experience and time, he also brought the tool that made everything possible. A Capstan winch that could bolt to his truck. This winch enabled us to do the work with just the two of us.
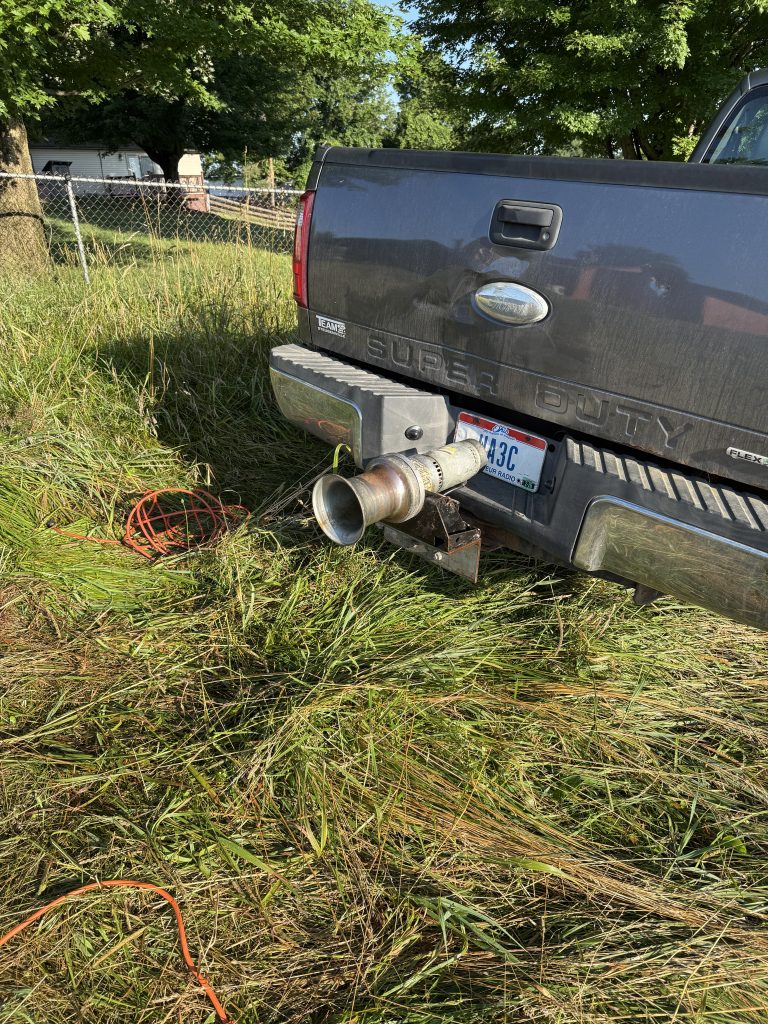
July 1, 2025
I know I have all the parts to build the station – I just have to find them and then modify things to fit the new situation. Today was guy wire day. I unrolled the Phillystran to know what I had and then started reworking the steel guy wires and insulators.
I chose guy wire lengths based on an NCJ article by N2IC. His analysis recommended lengths of less than 11′ or very
narrow guy-wire windows at approximately 28 and 41 feet. I wanted Phillystran down to about the 30′ level, then an 11′ section, and then 28′ sections as needed.
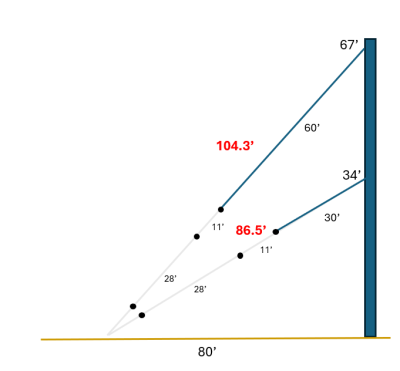
July 7, 2025
Mike arrived for our first session about 8 am on a morning that was boiling, humid, and calm. You could see the moisture in the pasture, and it was stifling as the sun warmed the air and pulled humidity up from the grass.
We started with the South tower. It was to be 70′ with guy wires at 34′ and 68′. It was a smooth process to rig the gin pole, pull up a section, bolt it on, and then repeat. We were ready for the first guy set after only 90 minutes of work.
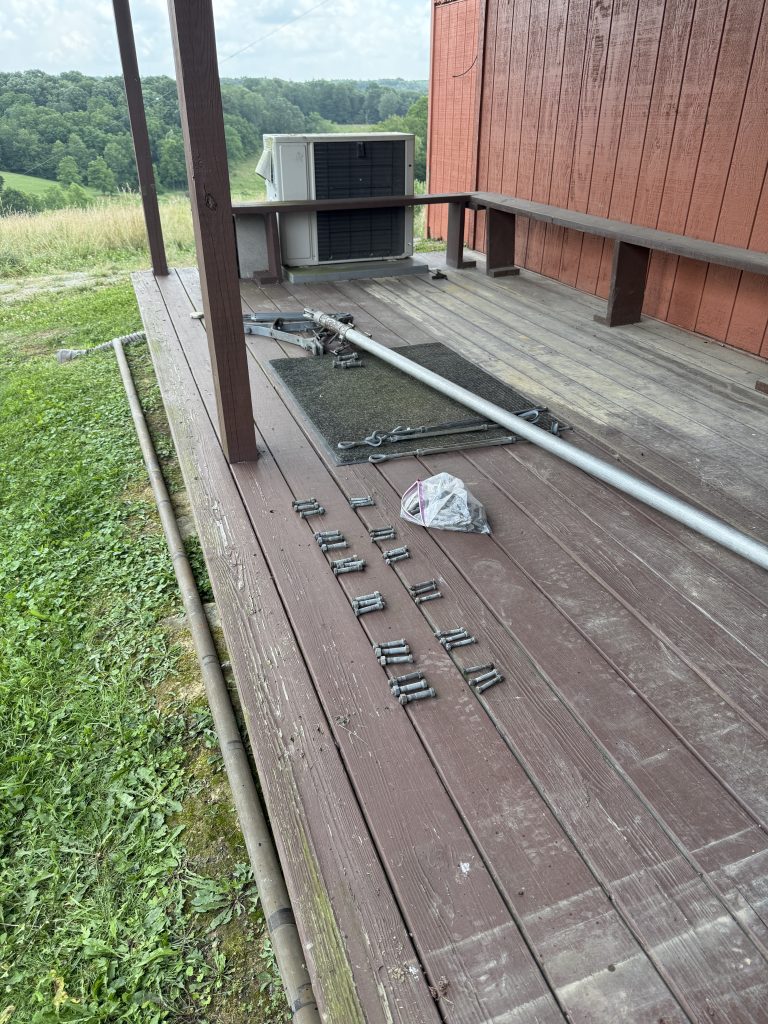
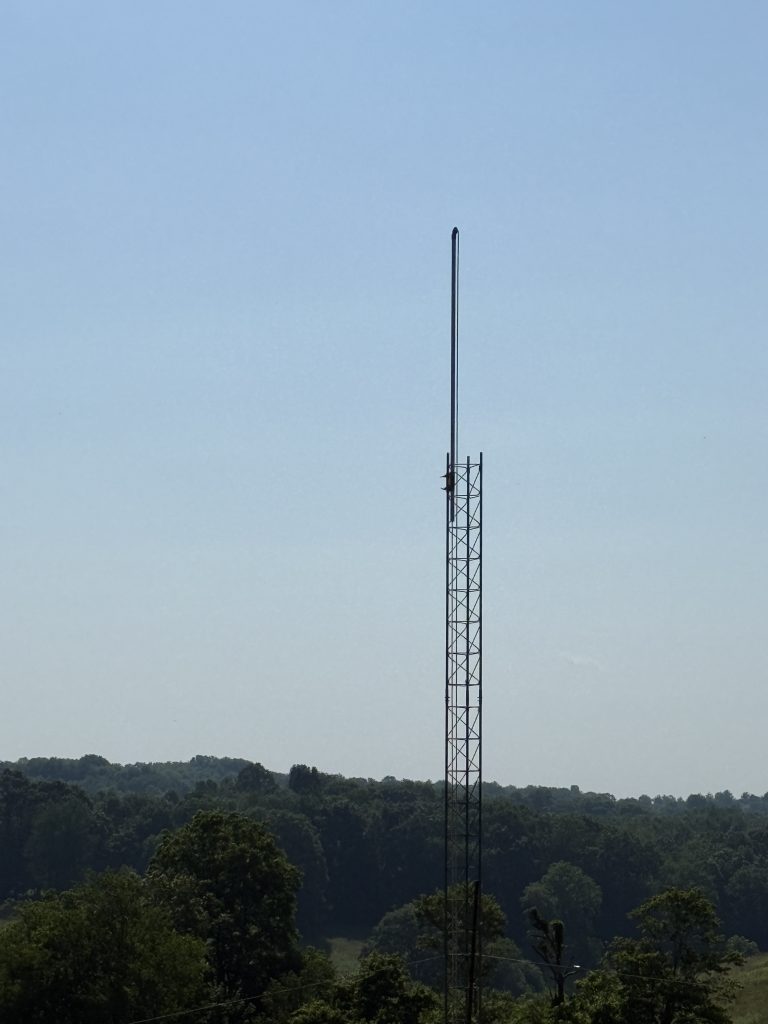
Mike introduced me to a clever way of installing the guy wires. He had three come-alongs so we could get each line tensioned before attaching it to the turnbuckle. (I had always done it by moving from guy anchor to anchor, tensioning each until everything was straight.)
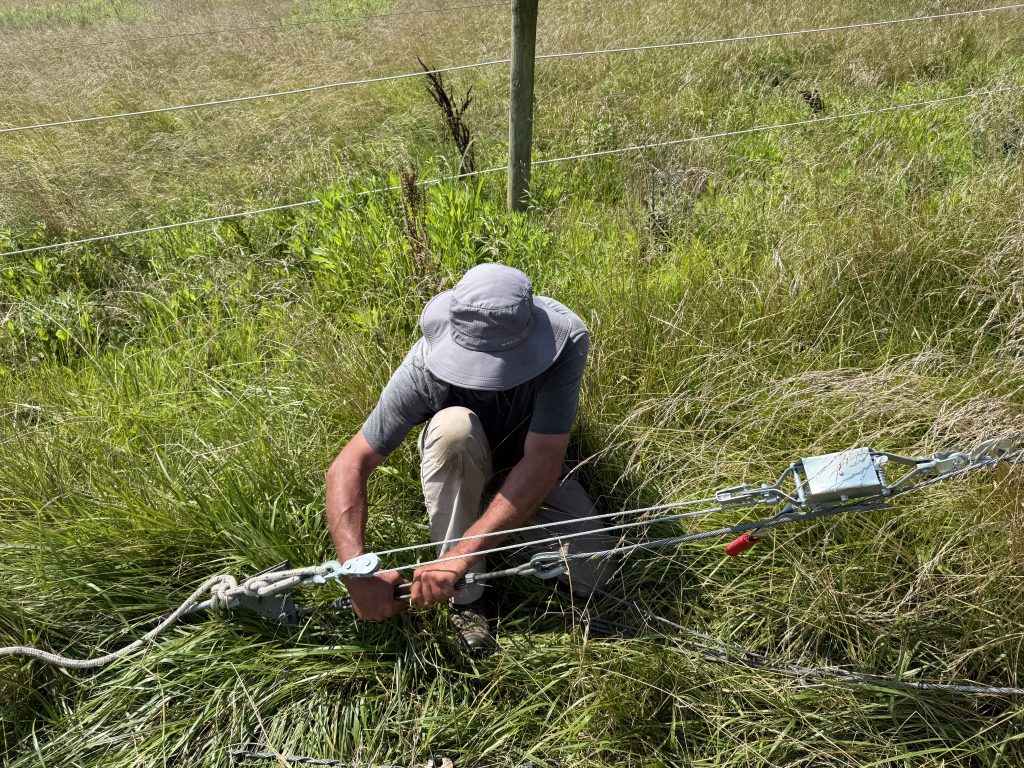
It was great to step back and see some progress.
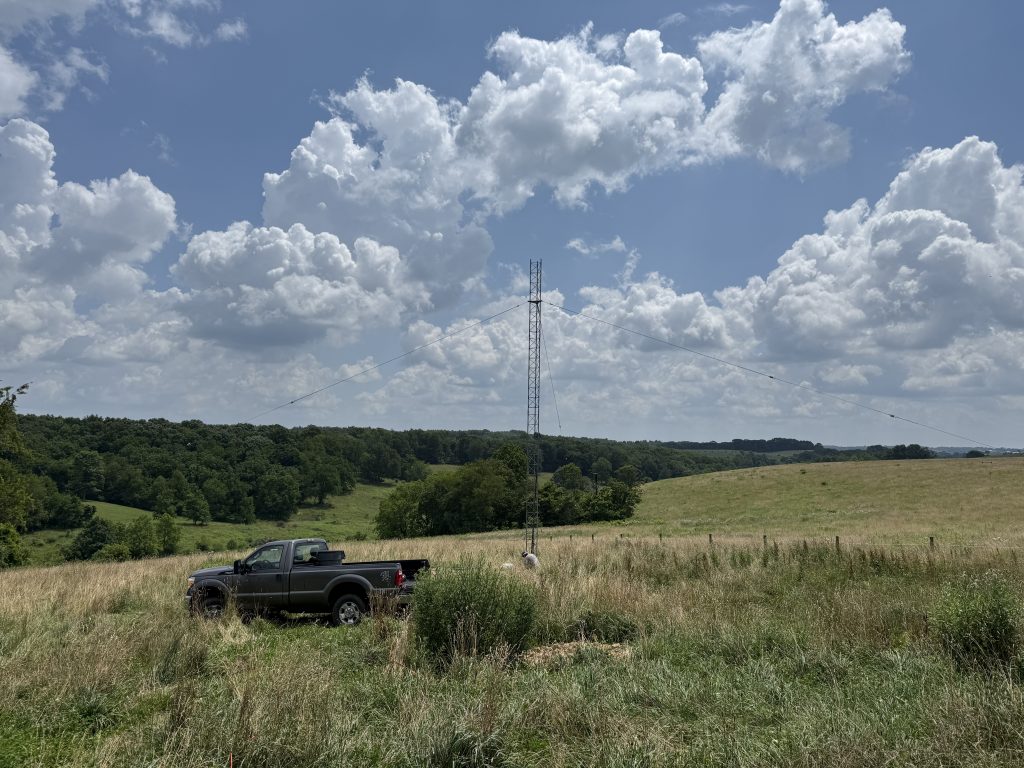
It was now almost 1 pm, and the heat was wearing on us. I normally do well with heat, but it was oppressive when working at ground level on the guy attachments. I decided I had had enough, and we called it a day.
July 10, 2025
We were back at it on a still warm and humid, but more cloudy morning a few days later. With just two of us, there aren’t many photos of the work in progress. I did grab this one as Mike was wrapping the rope on the winch to pull up a section.
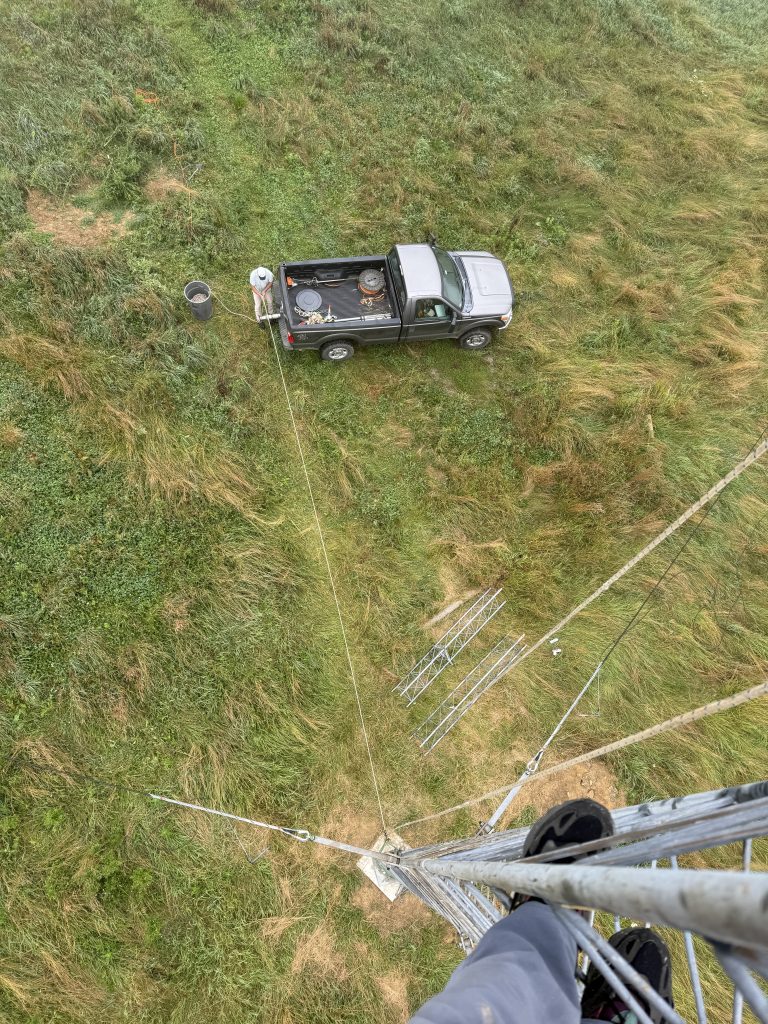
By 11:15 am, we had all the sections up and the second set of guy wires attached. Mike brought his Loos tension gauge so we could check the tensions. He also brought his transit. The result was a tower that felt very solid and was truly vertical!
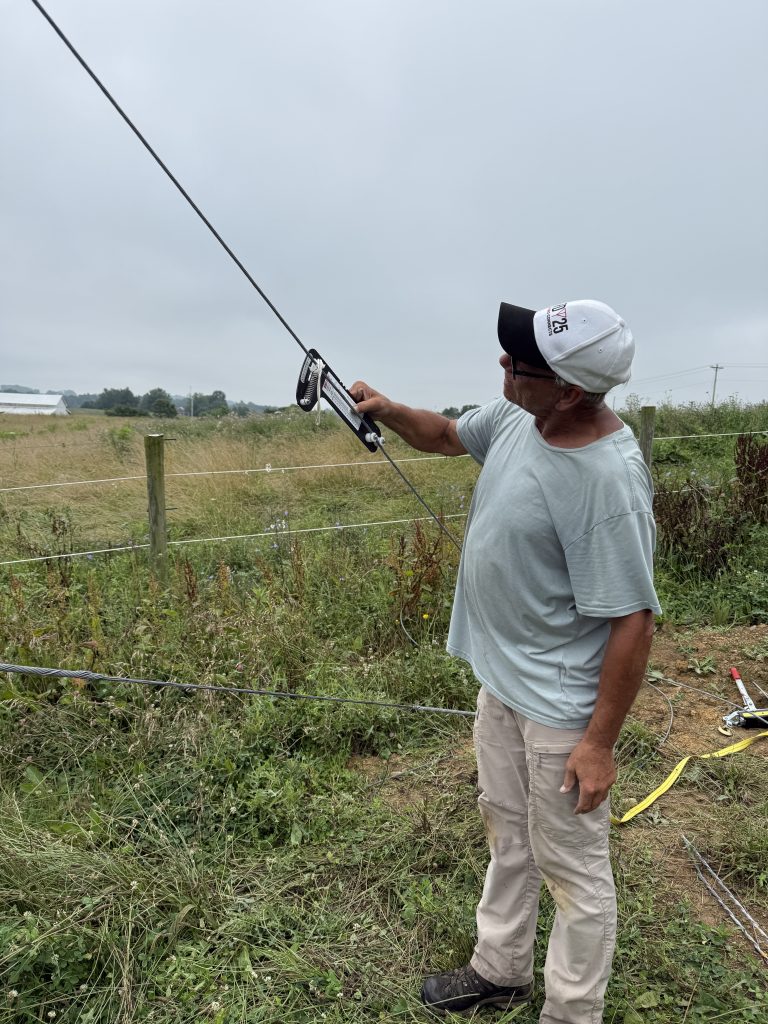
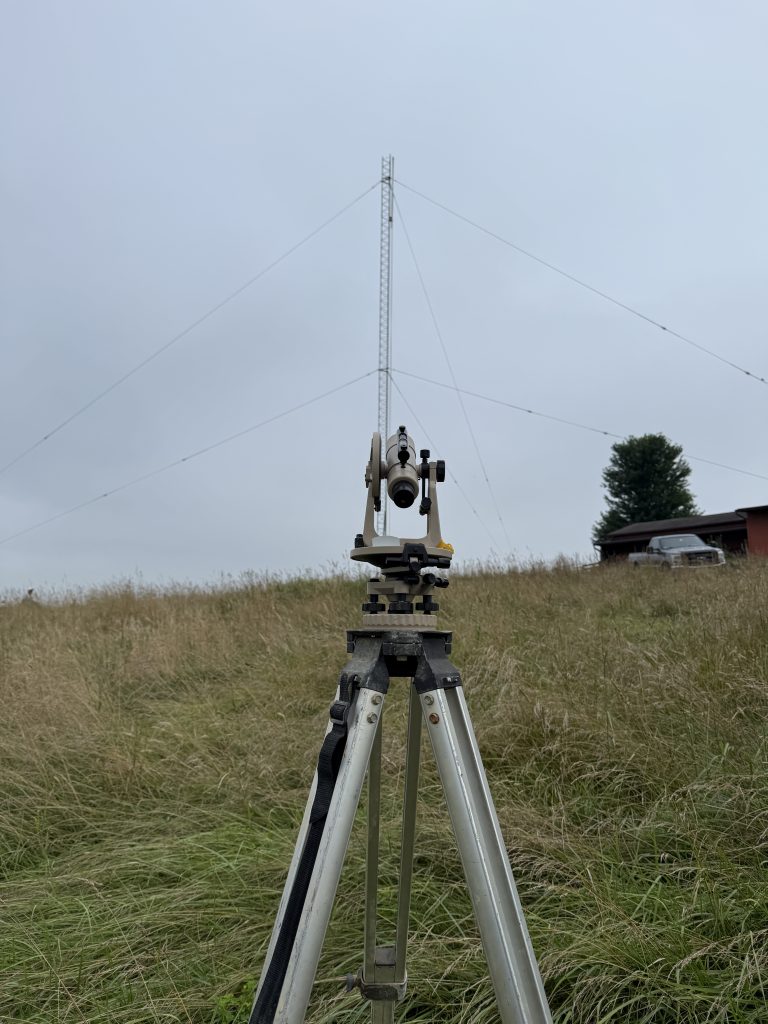
We added the top plate and called it a day at around 1 pm. I was thrilled to have this tower fully up in just two mornings of work.
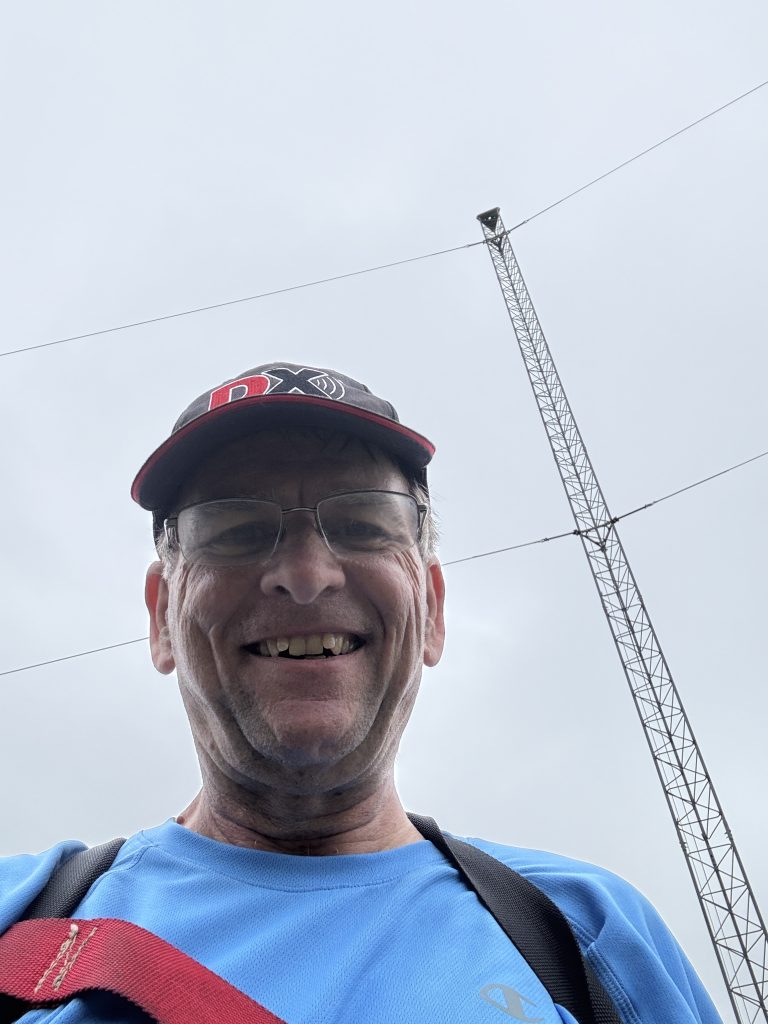
July 16, 2025
The heat and humidity finally broke, and we had a beautiful day to start work on the North tower. This one was to be 80′ with guy wires at 39′ and 78′.
We were getting pretty good at this and had the tower with the first set of guys up by 1 pm.
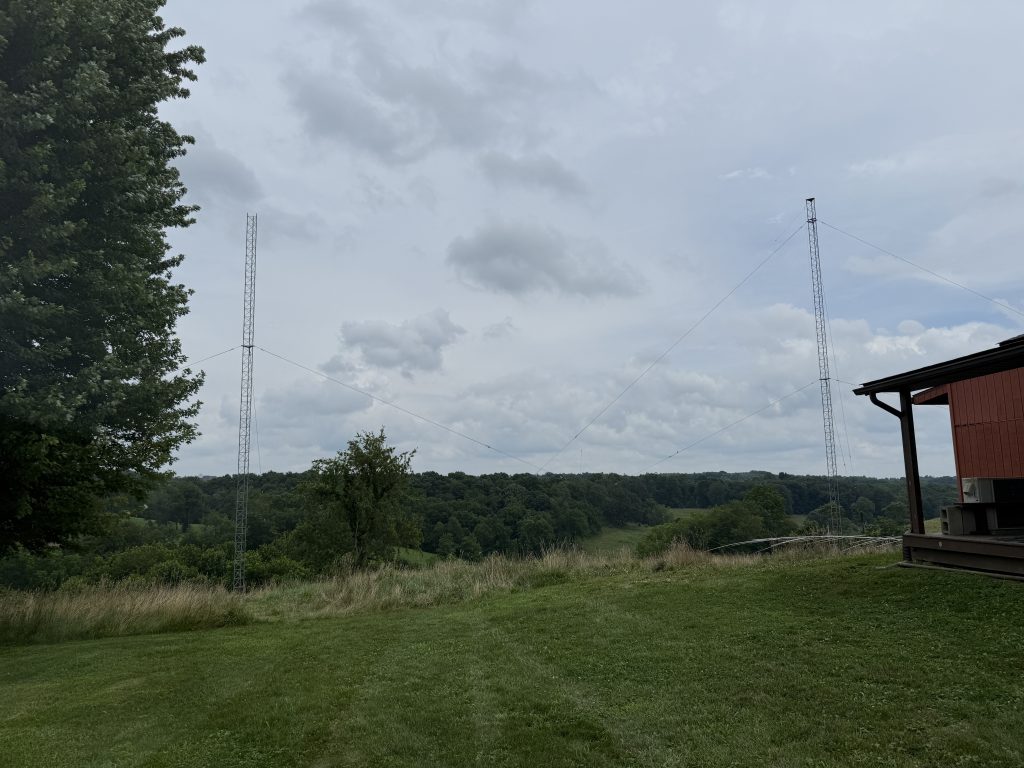
This tower will feature a 2-element 40m Moxon and a 5-element 20m Yagi antenna. Even with just two sections above the first guy point, I could feel things were wobbly. After a bit of thinking, it just seemed like it would be a risk to try to do this with only 2 guy sets. I had everything I needed to add another set, so I decided to rework things to have 3 guys at 25′, 52′, and 78′.
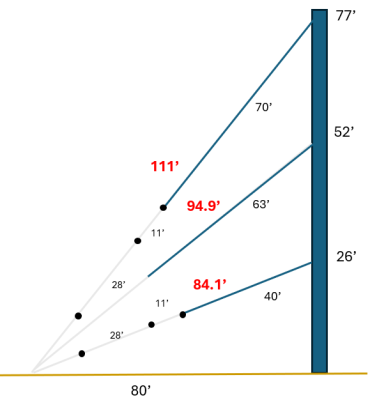
July 22, 2025
I was able to install the guy bracket at 50′ and loosely attach the guy set.
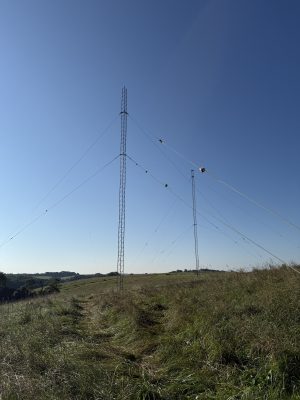
July 23, 2025
Mike arrived around 8 am, and I explained the change of plans for guying. I installed a guy bracket at 25′. We tightened the new set at 50′. That enabled me to remove the set at 35′ and move it down to the new bracket.
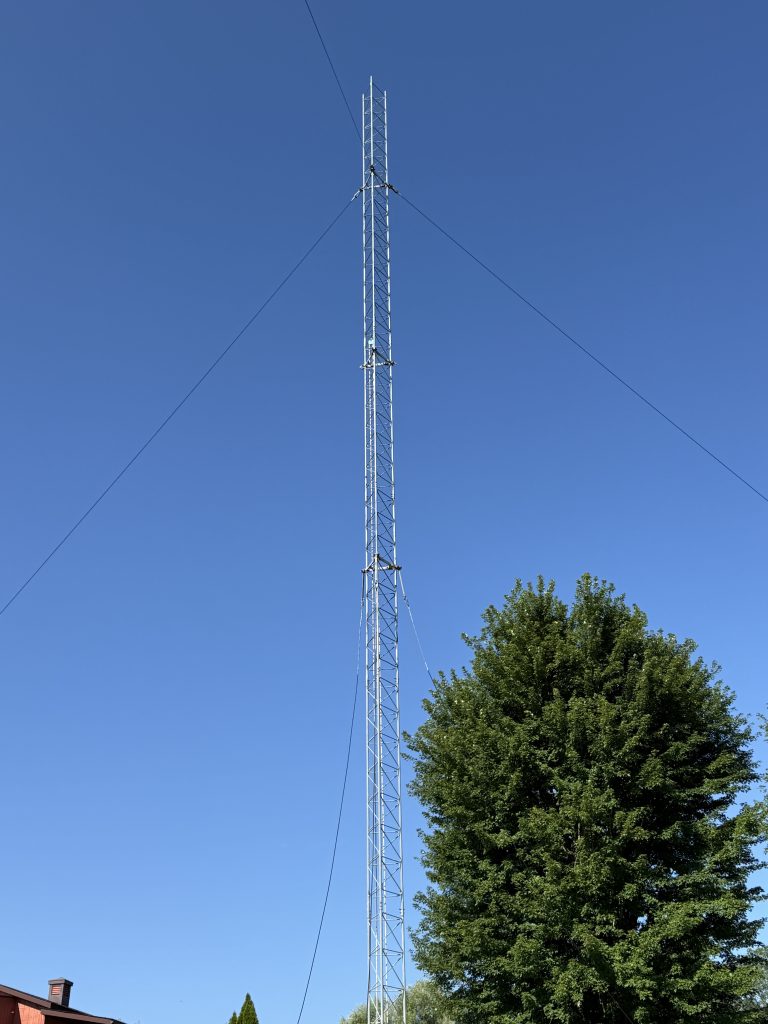
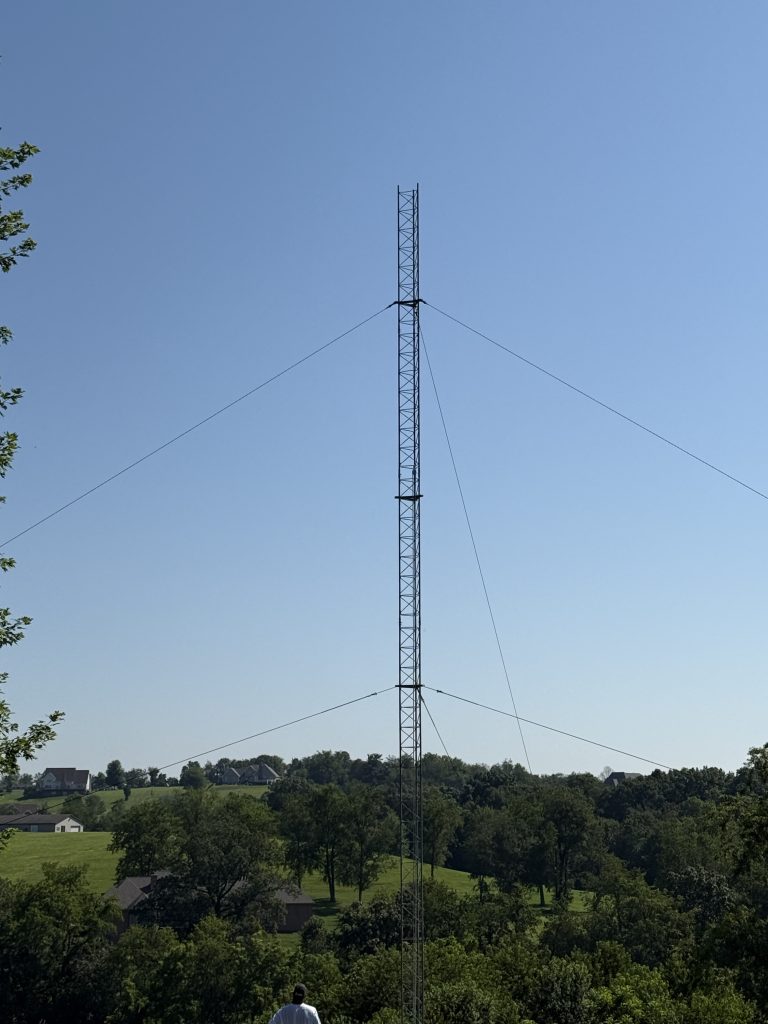
The bracket at 35′ could now move up to 78′ after two more sections were added. By 12:30 pm we had the tower fully up and guyed.
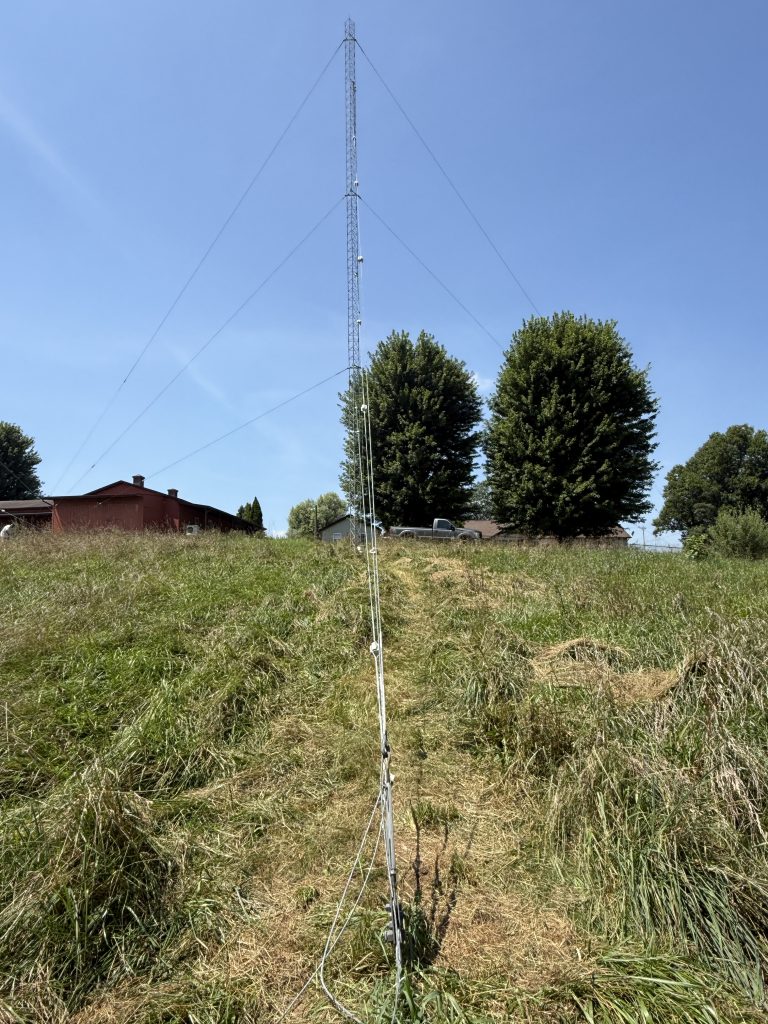
I had the C31xr assembled at the base of the other tower, and I had a Cushcraft A3WS 12/17m antenna also ready to go. Given the power of the Capstan winch, I asked Mike if he was game to make an attempt to raise antennas to the top of the south tower. He agreed, and we set a date.
If one tower is good, then two have to be better!
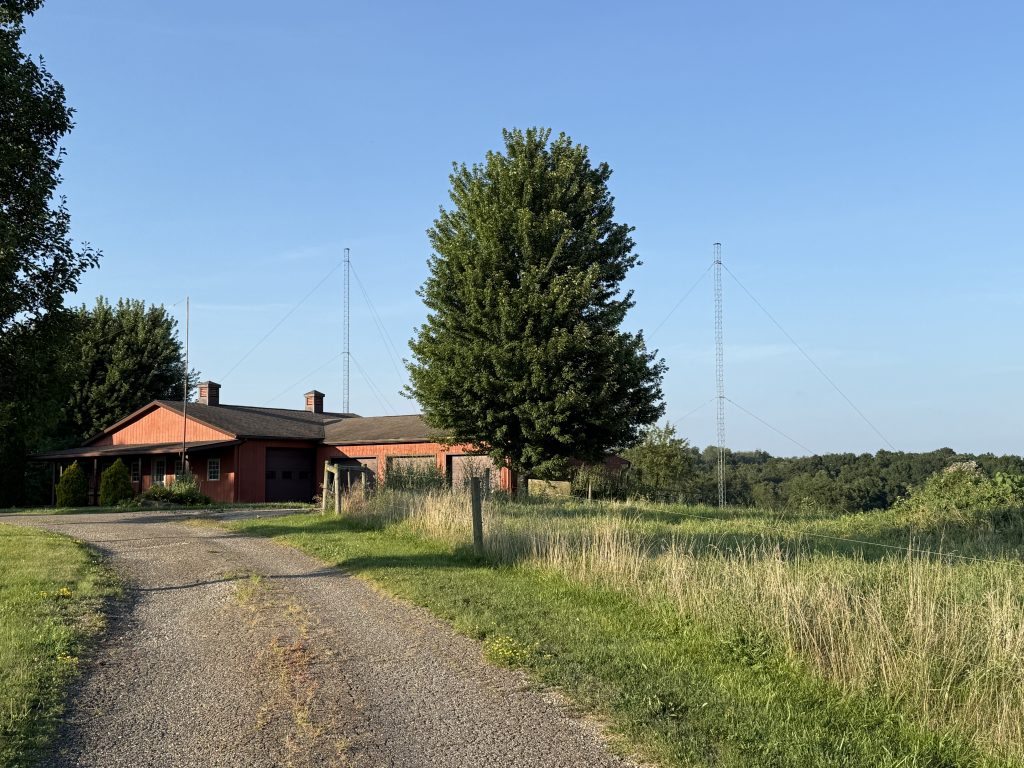